The TTC 2700 family consists of our largest high-end safety electronic control units designed to satisfy the upcoming needs of a wide range of applications in construction, agriculture, and special-type vehicles.
The free programmable control units can be programmed in C, and are equipped with a powerful Infineon TriCore™ Aurix™ TC399 processor featuring 6 x 32-bit Infineon TriCore™ cores (4-cores lockstep) and with 32MB ext. flash are protected by a compact, automotive-style housing suited for harsh environments. The controllers fulfill TueV Nord certified safety requirements up to:
- ASIL C (ISO 26262)
- SIL 2 (IEC 61508) / PL d (ISO 13849)
- AgPL d (EN ISO 25119)
- MPL d (ISO 19014)
- ASIL C (ISO 26262)
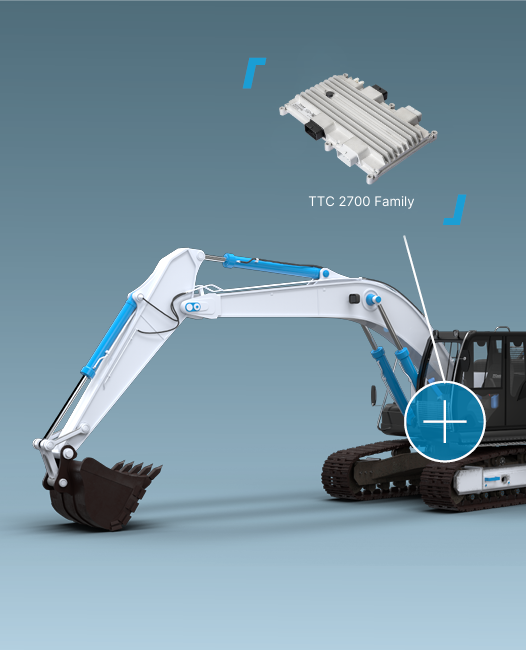
TTC 2700 control units are available in two variants:
Improved application development
The C programming environment is based on the PXROS real-time embedded operating system. This improves the traditional way of designing and writing an ECU application, allowing the split of the “main loop” user application into multiple working tasks that run until they are interrupted by a higher-priority task, blocked (waiting for an external event), or until a time limit expires. The efficient inter-task communication and synchronization mechanism using messages permits data to be safely transferred between tasks.
The 132 I/Os extensive set comes with various configuration options. Another use case is to build up a centralized architecture using one of the TTC 2740 / 2785 control units for the whole vehicle.
The 100BASE-TX (classic Ethernet) for TTC 2785 and the T1 (BroadR-Reach®) interfaces at TTC 2740 are available for application purposes, debugging, and application download, significantly reducing the time needed during the application development process or machine installation and commissioning.
Reduced connectivity costs and cabling weight
The 100Mbit/s speed of 100BASE-TX or 100BASE-T1 BroadR-Reach® (the evolution of traditional Ethernet, using unshielded single twisted pair cable, leading to reduced connectivity costs and cabling weight) allows much higher data throughput between different electronic devices (compared to traditional CAN or CAN-FD interfaces).
Reliable safety without compromise
The majority of the CPU-related self-tests needed to achieve the diagnostic coverage required for ASIL C are performed in hardware by the dual-core lockstep CPU. This ensures that much more processing power remains available for the application compared to solutions that implement safety measures in software. The available memory protection mechanisms allow the execution of safety and non-safety software on the same control unit without interference. The time-consuming validation of non-safe software is, therefore, no longer necessary. In case of safety-relevant failure, outputs can be shut off in 3 independent safety shut-off groups for output stages.
Key Benefits
The integrated real-time operating system (PXROS) with multicore support ensures a high level of application robustness and responsiveness, which is crucial for safety-critical applications.
The mixed-criticality support allows safety-related and non-safety-related code to run on the same CPU without reducing the overall safety level. This helps in lowering development costs and achieving faster time-to-market.
The TTC 2700 family products offer a highly configurable I/O set, including analog and digital timer inputs, HS PWM, and PVG outputs. This flexibility makes them suitable for controlling various hydraulic valves used in off-highway machinery.
Equipped with multiple high-speed interfaces such as CAN-FD, 100BASE-TX, and 100BASE T1, the TTC 2700 family products ensure reliable and efficient communication in distributed machine architectures.
The TTC 2700 Family features a high-performance Infineon AURIX™ TriCore™ CPU with 300 MHz, 6 cores (4 lockstep cores), and a Hardware Security Module. This ensures robust security for complex safety and security-relevant mobile machinery applications.
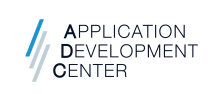
Enhance this hardware with dedicated software applications. We help OEMs throughout the entire machine development life cycle. Learn more and get in touch with our Application Development Center